Reducing Facade Construction Time with 3D Printing in Dubai
Architectural 3D printing in Dubai is transforming the construction industry by significantly reducing the time needed to build custom facades.

Architectural 3D printing in Dubai is transforming the construction industry by significantly reducing the time needed to build custom facades.
This innovative technology streamlines the design, production, and installation process, allowing architects and developers to complete projects faster. Dubai’s rapid urban growth demands efficient construction methods, making 3D printing a key solution for modern facade development.
Automated Fabrication Speeds Up Production
Traditional facade construction involves multiple manual processes, from molding to assembling individual components. 3D printing Dubai automates the entire process, producing facade sections layer by layer in a single operation. This eliminates delays caused by human labor and speeds up production.
Automation also reduces errors, ensuring precise designs with minimal rework. Faster production leads to quicker project completion, making 3D printing an ideal solution for Dubai’s fast-paced construction industry.
On-Site 3D Printing Eliminates Transportation Delays
Transporting facade components from factories to construction sites can cause delays. 3D printing allows for on-site production, eliminating the need for long-distance transportation. This is especially beneficial for large-scale projects that require custom facade elements.
By printing facades directly at the construction site, developers can avoid shipping disruptions, reduce costs, and maintain better control over the project timeline.
Rapid Prototyping Accelerates Design Approval
Before construction begins, architects often create prototypes to test facade designs. Traditional prototyping methods can take weeks, delaying the approval process. 3D printing enables rapid prototyping, allowing architects to produce and modify designs within hours.
This speeds up decision-making and reduces the time spent on design revisions. Developers can quickly visualize and approve facade elements, ensuring faster project progression.
Reduced Need for Molds and Formwork
Traditional facade construction relies on molds and formwork, which take time to create and adjust. 3D printing eliminates this requirement by directly printing facade elements in their final form.
Without the need for molds, construction teams can save weeks of preparation time. This makes 3D printing a highly efficient alternative for custom facades in Dubai’s architectural projects.
Parallel Processing for Multiple Facade Components
With traditional methods, different facade sections must be constructed sequentially. 3D printing allows multiple components to be produced simultaneously using multiple printers.
This parallel processing significantly reduces overall construction time. Large-scale projects can benefit from printing various sections at once, accelerating the completion of entire building facades.
Minimized Labor Requirements Speed Up Construction
Traditional facade construction requires skilled labor for cutting, assembling, and finishing materials. Finding and training workers takes time and adds to project delays.
3D printing reduces reliance on manual labor by automating most of the production process. This speeds up construction while lowering labor costs. In Dubai, where demand for skilled workers is high, 3D printing provides an efficient alternative.
Seamless Integration of Complex Designs
Custom facade designs often require extensive detailing, which can slow down construction. 3D printing simplifies the process by printing intricate patterns and geometries in one step.
With advanced software, architects can create complex designs without additional manufacturing time. This enables unique, customized facades without extending project deadlines.
Fast Drying and Curing of 3D Printed Materials
Traditional construction materials, such as concrete and plaster, require extended drying and curing times. 3D printing uses specially formulated materials that cure faster, reducing waiting periods.
Some 3D printed facades use quick-setting composites that harden within hours. This allows for faster installation and shorter project timelines.
Optimized Material Usage Reduces Rework
Material waste and miscalculations can cause delays in traditional construction. 3D printing optimizes material usage by precisely depositing the required amount, reducing errors and the need for corrections.
Less waste means fewer project setbacks. Developers can stay on schedule without unexpected material shortages or rework.
Pre-Assembled 3D Printed Facade Panels
3D printed facade panels can be prefabricated and delivered for quick installation. This reduces the time spent on assembling individual elements on-site.
Pre-assembled panels allow developers to complete facades in days instead of weeks. This is especially beneficial for large-scale projects in Dubai that require efficient construction methods.
Lower Risk of Weather-Related Delays
Weather conditions can slow down traditional facade construction. Rain, extreme heat, and sandstorms can disrupt labor and material handling.
3D printing is less affected by weather because it operates in controlled environments or automated settings. This ensures continuous production, keeping projects on track even in challenging conditions.
Government Support for Faster 3D Printing Adoption
Dubai’s government is actively promoting 3D printing in construction through policies and investments. Regulations are being adapted to streamline approval processes, further reducing delays.
With a strong push toward 3D printed buildings, developers can adopt the technology more easily. This results in faster project approvals and shorter construction timelines.
Real-World Examples of Faster 3D Printed Facade Construction in Dubai
Dubai has already implemented 3D printing in several projects to speed up construction. The Dubai Municipality’s 3D printed office building was completed in just 17 days. Such projects demonstrate how quickly facades can be produced and installed using 3D printing.
More developers are turning to 3D printing to meet tight deadlines without compromising quality. As the technology advances, even faster facade construction will become possible.
Future Innovations in 3D Printed Facades for Speed Optimization
The future of 3D printing in Dubai’s facade construction looks promising. Advancements in robotic printing, AI-driven designs, and smart materials will further reduce construction time.
New printing techniques, such as multi-material printing and ultra-fast curing compounds, will enable even quicker facade production. These innovations will set new benchmarks for speed and efficiency in Dubai’s construction industry.
Conclusion
Architectural 3D printing is transforming facade construction in Dubai by significantly reducing building time. Automation, on-site printing, rapid prototyping, and optimized material usage contribute to faster project completion.
With government support and ongoing technological advancements, 3D printing will continue to shape the future of Dubai’s skyline. Developers and architects who adopt this technology can complete projects faster while maintaining high-quality standards.
What's Your Reaction?
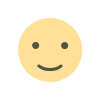


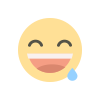

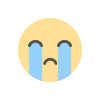
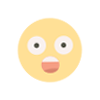